In the previous Section, we looked inside test equipment to see how it worked
and to understand its design limitations. We are now in a position to move
on, so this Section is concerned with using test equipment to bring a device
to a usable state.
There are three stages of testing:
-- Safety testing: Will the device under test (DUT) endanger the user?
-- Functionality testing: Does the DUT work as it should?
-- Faultfinding (hopefully optional): Having established that the DUT doesn't
work correctly, what needs to be fixed? Rather than scribbling results on scraps
of paper and losing them, you will find it extremely useful to keep a logbook
of your tests. The logbook should include:
-- Circuit diagrams of the circuit tested
-- Diagram or description of how the test was undertaken
-- Results of the test
-- Subjective comments on the test (Were the results expected?)
-- Date of the test, and test equipment used
-- If any of the test data has been saved to computer (spread sheet, photograph,
etc.), include the file names.
The purpose of the logbook is to enable you to look back and know the results
of a test, rather than scratching your head and saying, ''I'm sure I've tested
this before. ''
Safety
Before we go any further, we should understand that there is no such thing
as perfect safety. Everything we do, from crossing the road to eating a chicken
sandwich carries an element of risk.
Lawyers currently enjoy a climate where ludicrous damages are awarded to clients
who failed to take any responsibility for their own safety - of course a cup
of hot coffee will scald you if you spill it over yourself! The dangers of
hot liquids are well known, but the dangers of tube electronics are not as
well known as they used to be, and even professional engineers can become complacent
about putting their hands inside live equipment.
The aim of this section is to point out some of the more common dangers and
show simple ways by which risk may be reduced.
Nevertheless, it is impossible to cover all possible situations, and this
is why electronics workshops forbid work on live equipment unless two people
are present. In that way, one person is ready to rescue the other in the event
of an accident. If you have a more experienced friend, it would be a good idea
to emulate commercial practice by asking them to attend when live working is
necessary and to check your work beforehand. Ensure that they know how to switch
off the power quickly.
An understanding of the physiological effects of electric shock, whilst somewhat
ghoulish, serves to underline why safety is so important.
How an electric shock can be received
The best way of avoiding electric shock is to understand how it can be received.
The electricity supply leaving the wall socket in your home is a very good
approximation to a pure Thevenin source of zero resistance, with one side of
the source connected to ground. In this instance, we do not mean ground in
its purely technical sense, the supply really is connected to the planet Ground.
You and I perform most of our activities on the surface of the ground, and
we are therefore electrically connected to it, albeit usually by a high-resistance
path. We can improve our electrical contact to ground by standing barefoot
on a damp floor, or by firmly gripping something that is electrically bonded
to ground.
Manual activities like hobbies are precisely that, manual. They involve our
hands going inside objects, and touching them.
Humans generally possess two hands, and so what is more natural than to put
both hands inside a piece of equipment? The scene has now been set for one
hand to be holding the (grounded) chassis of a piece of equipment, whilst the
other is moving around and accidentally comes into contact with live mains.
Look at your hands. They are on the ends of your arms, and your arms are joined
to your torso. Trace a line from the fingers of one hand to the fingers of
your other hand, without the line leaving your body. Note the path.
The easiest path for an electric current to flow from one hand to the other
crosses near the heart. Similarly, a shock from one hand to ground passes near
to the heart.
The effects of electric shock
The main danger from electric shock is fibrillation of the heart.
The heart normally beats at a slow pace regulated by electrical impulses from
the brain. If we apply 230V 50Hz to the heart, it pulses quickly, the flow
regulating tubes do not operate correctly, and no blood is pumped, leaving
the brain to die of oxygen starvation in about 10minutes. A sustained current
of 20mA through the heart is sufficient to cause fibrillation, resulting in
the adages, ''20 mills kills'', and, ''it's the volts that jolts, but the mills
that kills''.
A sustained current might not kill, but could cause irreversible injury due
to the heating effect of the current. RF burns are notorious for this, and
can result in limbs having to be amputated to prevent the spread of gangrene.
A lower sustained current may cause injury from which the victim does recover.
Eventually. Skin grafts may be necessary.
A current of 20mA results from a 230V supply connected across a resistance
of ~11 kOhm. Very few power supplies have a source resistance as high as this,
so shock current is determined primarily by skin resistance, and a shock from
a puny transformer delivering 230V is just as dangerous as the shock received
directly from a 100A mains feeder. Skin resistance is reduced by damp hands,
and standing in the rain in a puddle of water lowers resistance further.
All of the above considerations refer to the direct consequences of electric
shock, but do not consider secondary effects. A minor shock that causes the
victim to lose their footing and fall over could be fatal if they happen to
be standing on a ladder 30 ft above concrete. Another possibility is that the
reflex muscle jerk in reaction to the shock could cause the victim to throw
them selves through a glass window and bleed to death.
Even after a minor electric shock, the victim will be confused and disoriented,
and shock in its full medical sense is a possibility. Shock kills.
Burns
Although the primary hazard of electrical equipment is shock from high voltages,
it should be realised that low voltages can be just as hazardous. A low-voltage/high-current
DC supply will have a large, low ESR, reservoir capacitor capable of delivering
many amps of current into a short circuit.
Rechargeable batteries are even more dangerous because they are capable of
sourcing substantial current for a significant time. (Think about it, a car
starter motor requires 100A, or more, for several seconds.) These batteries
are not merely capable of burning, they can vaporize metal bracelets, watch
straps, and tools. Do not wear jewelry whilst working on live equipment.
Avoiding shock and burns
It should now be obvious that electric shock is potentially lethal, burns
can be serious, and that both must be avoided at all costs.
Provided that you have made, or modified, your equipment carefully, there
will be no exposed voltages, and all metalwork will be grounded, resulting
in a very low risk of shock. The danger arises when you deliberately remove
the safety covers, and start testing the equipment with power applied.
Some authorities suggest that you should always work on live equipment with
your left arm behind your back, so that any shock received will not pass from
arm to arm across the heart.
Whilst it is true that this will reduce the severity of the shock, it tends
to increase the risk of receiving a shock.
The best way of improving safety is to think about safety, and to think about
what you are doing. It might seem obvious to think about what you are doing,
but for most of our lives we think about many things at once. For instance,
when driving, are you thinking only about driving, or are you actually thinking
about what you are going to say to your boss when you arrive late for work,
and when is that idiot in front of you going to turn into the junction, and
isn't that a rather attractive male/female/alien over there by the bus stop?
Thinking about what you are doing means not working late. Do not attempt to
test a newly completed project at 11:30 at night; you will not be alert and
could damage the project and/or yourself.
Electrical safety testing
Consumer electronics falls into two safety categories. Class I has an grounded
conductive barrier enclosing the high voltages, whereas Class II has two independent
insulating barriers enclosing the high voltages. Many appliances are actually
a combination of the two categories because although the appliance could be
Class I, the mains lead is invariably Class II.
Class I relies on quickly blowing the mains fuse, whereas Class II relies
on undamaged barriers. Commercial safety testing therefore consists of a careful
inspection by a competent person to check barrier integrity, plug wiring, and
that the correct fuse has been fitted. These visual tests are backed up by
electrical tests.
A safe piece of Class I equipment has an grounded conductive barrier with
no conductive path to any of the enclosed high voltages and a sufficiently
low-resistance path to ground that any contact to the mains line causes such
a large current to flow that the mains fuse ruptures quickly. Electrical safety
can there fore be tested by measuring leakage current flowing from the barrier
and by measuring the resistance from the barrier to the ground pin of the mains
plug. Since many pieces of equipment have to be tested, it makes sense to have
a dedicated instrument to make the tests.
Portable appliance testers
Portable appliance testers (PAT) are simply specialized resistance and leakage
testers with appropriate connectors for quickly testing mains portable appliances.
The emphasis on the word ''quickly'' is important because even a small business
could have hundreds of appliances that must be tested for safety each year.
In order to cause minimum disruption each appliance must be tested quickly
and unambiguously, and a record must be made of the test. Older PAT testers
simply make the required pass/fail electrical tests, whereas newer testers
guide the operator through the test procedure, make the measurements, give
pass/ fail status, and log the data together with the appliance's identification
(often a bar code) for later download to a computer.
Because the newer testers make it much easier to comply with the various safety
regulations, there are plenty of older, manual testers available in perfectly
good working order, and you might want to acquire one (see FIG. 1).
As part of a Class I test, a PAT tester measures ground loop resistance (resistance
from the chassis to the ground pin of the plug) by passing a considerable current,
sometimes as much as 25A. The purpose of such a large test current is to detect
frayed ground connections. A single strand would still have low resistance
because it would be very short, even though its cross-sectional area would
be small, so a simple resistance measurement could not detect the problem.
However, the PAT tester deliberately seeks to rupture such frayed connections,
which subsequently fail the resistance test. At the same time, the tester applies
a high voltage (>500VRMS) simultaneously to the line and neutral terminals
and monitors leakage current returning through the ground circuit. Do not touch
the appliance whilst the PAT tester applies this dangerous voltage.
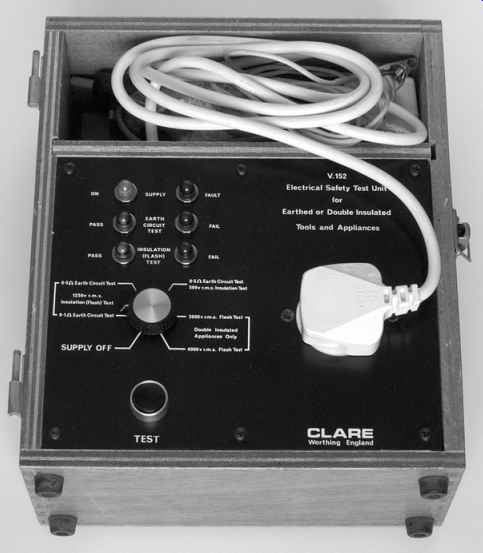
FIG. 1 Older PAT testers are still perfectly capable of making important
safety tests.
Be aware that PAT testers are not invincible, and can develop faults just
like any other piece of equipment. If you rely on a tester to determine safety
of other equipment you have to be certain that the tester works correctly and
that you are operating it correctly. Most testers include operating instructions
and a selection of ''faulty'' test jigs that should be regularly tested to
verify correct operation of the tester. You might question the validity of
using a second-hand tester, particularly since it will almost certainly be
sold without any warranty of fitness for purpose. Provided that you are not
using it to assist in selling goods or services, the question is not whether
the tester perfectly meets all the latest safety regulations, but whether it
reduces risk compared to not being able to test at all.
Functionality testing
The word ''testing'' implies a degree of ambiguity about the results of the
test; if we knew that our new amplifier was going to work perfectly from the
moment that it was completed, we would not need to test it. However, we know
that wiring mistakes can be made, and that components could be faulty, so we
test our amplifier carefully.
Second-hand equipment versus freshly constructed new equipment
Both types of equipment should be treated with a great deal of suspicion and
apprehension. The only sensible state of mind when first switching on is controlled
fear.
Quite clearly, a piece of newly constructed equipment will be switched on
at some point, but some old equipment may be so dangerous, or riddled with
faults, that it should never be energized, other than applying kinetic energy
to throw it into a skip.
The state of old equipment can easily be determined by looking at the components.
Things to avoid are:
-- Wire insulated with rubber and covered with cotton
-- Enormous resistors marked with tip, body, and spot color codes
-- Electrolytic capacitors with bulges in the rubber surface supporting the
tags
-- Previous evidence of fire
-- Insulating tape anywhere!
Vintage radios may incorporate any or all of these features but may still
be of value to someone, so try to check with someone else before destroying
them [1].
For a professional, the worst possible sign is previous modification by an
amateur. The professional then has to decide whether or not the amateur knew
what they were doing. What is the effect of their modification, and was it
done competently and safely? For this reason, modified equipment is usually
worth less than unmodified equipment, so bear this in mind before you embark
on modifications.
Second-hand equipment can often be dated by the date on the electrolytic capacitors.
If it is over 30 years old, it is likely to need major refurbishment even to
make it work, so this should be taken into account if you are considering purchase.
The first application of power
Before applying power for the first time, the following ''Ten Commandments''
should be observed:
-- Inspect the ground bonding. Does the chassis appear to be properly grounded?
(Does an undamaged ground wire make a good connection to the chassis? If a
tag is used, is it tightly bonded with a star washer between it and the chassis?)
-- When measured, is the resistance from the ground pin of the mains plug
to the chassis of the equipment significantly less than 0.5 Ohm? (Preferably
use a PAT tester.)
-- With the power switch on the equipment (if fitted) switched on, is the
resistance from the other pins of the mains plug to the ground pin infinite?
(Preferably use a PAT tester.)
-- Does the mains cable look safe? i.e. not frayed, perished, cut, or melted
by a soldering iron.
-- Is the mains plug wired correctly?
-- Does the plug grip the sheath of the cable correctly?
-- Does the plug look safe? i.e. no cracks, chips, dirty pins, etc.
-- Is a fuse of appropriate rating fitted? (It is unlikely that the fuse rating
should be greater than 3A.)
-- Does all the internal wiring of the chassis look secure?
-- Is the chassis clear of swarf and odd off-cuts of wire? Turn it so that
bits can fall out, and give it a really good shake, whilst blowing vigorously
into the chassis to free small parts. Alternatively, if it is too heavy to
lift and shake, use a 1/2" paintbrush and a powerful vacuum cleaner to
remove debris.
If all appears to be well, you can move on to the next stage.
The author always assumes that when power is applied, the amplifier will explode,
or at the very least, catch fire. It does not, therefore, make sense to stand
with your face over the amplifier, or to place it in the middle of a pile of
inflammable debris. Power amplifiers should have dummy loads, or ''disposable''
(cheap) loudspeakers should be connected across their outputs.
The safest way to test a tube amplifier is in stages. Many amplifiers use
a tube HT rectifier, so if this is removed, the mains transformer and heaters
can be tested before applying HT. Silicon HT rectifiers make disabling the
HT a little harder, and require the AC to the rectifiers to be removed. If
this is a new amplifier, you will have planned ahead by testing the heaters
before doing any other wiring (that way, the heater wiring is easily accessible
should a fault surface).
The heaters in indirectly heated tubes take a moment before they begin to
glow, so connect a meter across the heater supply to give an instant indication
of whether the heater supply is present, and leave the meter in a clearly visible
position. If you have a variac, you can apply power gently, and if the meter
monitoring the heater supply doesn't immediately respond when you advance the
variac from zero, back it off and investigate.
The advantage of using a variac is that even a short circuit across the heater
supply would be unlikely to cause damage because you would spot it before applying
significant voltage.
If you don't have a variac, retire to a safe distance and apply the power
in silence. This way, you will hear any unusual noises, such as the crackles
or pops that presage destruction.
If the meter monitoring the heater supply responds appropriately and nothing
untoward happens, move a little closer and sniff the air. Can you smell burning?
Are there any little wisps of smoke leaving the chassis? If all still seems
to be well, look closely at the heaters -- they should be glowing, but should
not have hotspots (see FIG. 2).
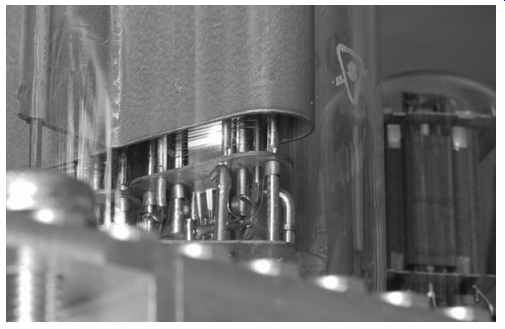
FIG. 2 This 13E1 had a nasty cathode hotspot, so it was rejected without
HT ever being applied to its anode.
Leave the tubes to warm for a while. Ideally, at first switch-on, unused tubes
should warm their heaters for 30minutes before HT is applied. However, even
10 minutes gives time for your nerves to calm down and for you to consider
your next step.
Having left the heaters glowing for a while, check the temperature of the
mains transformer, which should be cool. Switch off power, and unplug the mains
lead, leaving it in plain sight. If the amplifier has heater regulators, carefully
inspect them for signs of damage, but be careful near the tubes, which will
still be hot.
If nothing has been damaged by warming the heaters, it is time to test the
HT as well as the heater supplies. Depending on the complexity or output power
of the amplifier, this might be done in a number of ways:
-- Classic amplifiers simply need their HT rectifier to be inserted and the
amplifier to be switched on.
-- Modern amplifiers often use silicon HT rectifiers. Suddenly applying peak
HT to an electrolytic that has sat quietly on a shelf for several months is
unkind. Use a variac to bring the voltage up gently over 20 seconds, or more.
-- If the amplifier has separate HT and heater transformers, it is worth powering
the HT transformer from a variac and testing the HT before completing the final
wiring that connects the transformer to the amplifier's internal mains distribution.
Individual circumstances will determine how you test the HT for the first
time, but if it's possible to do it gently, then do so -- it minimizes the
amount of smoke.
Having chosen your method of testing the HT, apply power.
Listen. Are the loudspeakers making any unusual noises? In this instance,
silence really is golden. Is the HT voltage correct? If the HT voltage is correct,
then it is highly likely that the circuit is working as it should, and you
may breathe a quiet sigh of relief.
If you are testing a newly built power amplifier, there is a 50/50 chance
that global negative feedback taken from the loud speaker output will turn
out to be positive feedback, and the amplifier will become a power oscillator.
Often, before oscillation starts, a quickly increasing hum will be heard from
the loudspeaker; if the amplifier is switched off at this point, only a brief
shriek of oscillation will be suffered.
If, at any point, something untoward happens, switch off immediately at the
mains outlet and unplug the mains plug.
Usually, if anything is wrong in an electronic circuit, heat is generated
and components are burnt, so look for charred resistors or wires. Once the
burnt parts are found, the fault is usually blindingly obvious.
If you switched off hurriedly because of a burning smell, what sort of a smell
was it? Old equipment will often be dusty, so a slight burnt dust smell is
normal. Bacon smells are sometimes produced by burning mains transformers,
whereas burning PCBs often smell like underground railway stations with a hint
of charcoal, but burning wiring gives off an acrid smell.
If the amplifier appeared to be satisfactory, leave it switched on for a minute
or two longer, whilst keeping an eagle eye on everything; particularly output
tubes, which should not have glowing anodes, or purple and white flashes. Switch
off and sniff the internals closely for unusual smells. Some engineers go one
step further and touch components with their finger to check temperature, but
this is not recommended as some HT may still be present. If all seems well,
the amplifier can be switched on again, and all the DC voltages carefully checked,
if it still looks good, then it probably is good.
If you have a variac, now is the time to check how well the amplifier responds
to mains voltage variations. UK mains voltage is specified as being 230V +10%
-6%, but this is simply a paperwork ruse to enable harmonization with the rest
of the European Union. In practice, the voltage at your wall socket is the
same voltage it always was. Nevertheless, although mains voltage variations
are smaller than they used to be, the voltage does vary, and could cause problems.
Use the variac to check that capacitor voltage limits are not exceeded when
253V is applied, and that regulators don't become excessively hot.
Similarly, drop the mains voltage to 216V and check that regulators do not
drop out. These two tests are quite severe, and if you know that your mains
voltage is more stable, you might decide to adopt a less stringent test.
For the first few weeks of service, a new amplifier should be watched like
a hawk for signs of incipient self-immolation and should not be left unattended
when switched on.
Fault-finding
Unfortunately, we all have to do some faultfinding at some time or another,
either because we made a design or construction mistake, or because we need
to repair an amplifier that has failed due to old age. Before we dive into
details, we should ask one very important question, ''Did it work once?'' If
it worked once, you are looking for a faulty joint or component, and the resistance
range of your multimeter will prove invaluable for finding carbon resistors
that have ''gone high'' in value from age, or capacitors that have become leaky.
If the circuit is freshly built, then you are probably looking for a wiring
error.
Individually test each component
One way of faultfinding an amplifier might be to remove each component individually
and test it:
-- Resistors: Check claimed value against measured value using the resistance
range of a DVM.
-- Capacitors: Use DVM on resistance range to check for leakage, then check
claimed value of capacitance against measured value on the capacitance range
of the component bridge.
-- Inductors: Use DVM on resistance range to check continuity, then measure
inductance on the component bridge.
-- Valves: Use tube tester to compare with test data on the tube tester.
-- Semiconductor diodes: Use diode check range on DVM to check for open circuit
when reverse biased, and correct for ward drop when forward biased.
-- Transistors: Use a semiconductor analyzer to check functionality and compare
measured hFE with manufacturer's data.
Even better, use a curve tracer to plot its full characteristics.
-- Transformers: Connect to an oscillator and check each output with an oscilloscope
to verify functionality and turns ratio.
You will notice that the previous tests assume that you have a great deal
of expensive test equipment and full manufacturer's data to check your measurements
against. We only remove and test each component fully when:
-- We know no better
-- All else has failed.
The very best piece of test gear is your brain. It's readily available, so
it seems a shame not to use it.
DC conditions
The most common fault is a lack of signal, or reduced signal accompanied by
gross distortion.
Most faults can be found very quickly by measuring the DC conditions of the
circuit. For a well-designed circuit to be observably faulty, the DC voltages
usually need to be very wrong. Consequently, checking the measured voltages
against the design voltages quickly pinpoints the fault - it's easy to confuse
resistor multiplier band colors. Mark the measured voltages (lightly, in pencil)
on the circuit diagram. This usually has the effect of making the fault appear
blindingly obvious.
Sometimes you will not have the circuit diagram of the amplifier, let alone
its design voltages. No matter, there were very few variations in classic tube
circuitry, and their circuits were so simple that it is not difficult to produce
a block diagram of the amplifier. At this point, consider how you would design
an amplifier using those tubes, and look for similarities in the actual amplifier.
It should now be possible to obtain a rough idea of what sensible voltages
might be, and these can be checked against the faulty circuit. Modern amplifiers
are likely to be more complex and contain transistors, so they may require
careful circuit tracing. Fortunately, there are now so many websites carrying
information on tube audio that it is highly likely that the information you
need is somewhere on the web -- you just have to find it. If you can't find
a complete circuit diagram, tube data sheets are a good second best because
they give maximum ratings, typical applications, and pin connections.
A calculator is invaluable for calculating currents through resistors, and
generally deciding whether measured voltages make sense.
Do not implicitly believe what your digital voltmeter tells you.
Even the standard 10 M-ohm input impedance of a digital volt meter loads some
circuits, particularly the grid circuit of cathode followers or circuits with
grid battery bias. The author was once convinced that audible distortion was
due to the DC conditions within a tube active crossover, and a digital volt
meter appeared to confirm the theory, but a tube voltmeter with 90 M-ohm input
resistance measured a more correct value, and the distortion finally turned
out to be due to an intermittently scraping voice coil in a loudspeaker.
Blocks and attitudes
Imagine that you have just been told that the Hi-Fi isn't working. If you
have simultaneously been plunged into darkness, you assume that the power has
failed. Alternatively, if you look at the CD player, and see that its display
isn't counting, despite you having pressed ''play'', you conclude that either
the player or the CD is faulty, and you try another CD. In each instance you
are breaking the system down into blocks and checking each block. Exactly the
same technique can be applied to internal electronic faultfinding.
A power amplifier example
Imagine that you switch the amplifier on, play a CD, yet nothing comes out
of the loudspeakers. You look at the amplifier and observe that the heaters
are glowing. You have just eliminated the mains lead and associated fuse. Next,
it could be that the amplifier simply isn't receiving any signal, or that the
loudspeakers have become disconnected. Of course, the loudspeakers could be
faulty, but most loudspeakers contain two drive units, and possibly more, so
for both loudspeakers to be faulty, you require four simultaneous failures.
That just isn't likely, even if you had a very good party the night before.
Similarly, although the leads to both loudspeakers could both be faulty, it's
unlikely. It is far more likely that we are looking for a single fault that
affects both channels.
We ought to check that a signal is reaching the amplifier. We could try a
different source, or if the CD player has an integral volume control (and some
do), we could plug it directly into the power amplifier and increase the volume
gently from zero.
Assuming that there is still no sound, we know that we are looking for something
that is common to both channels and that's usually the power supply. We know
that the heaters work, so that narrows the investigation to the HT supply.
There haven't been any nasty smells, explosions, or fizzing noises, so something
has died quietly and completely. If a component was merely poorly, we would
have had low HT, and the amplifier would have produced some sound, although
probably very distorted.
All HT rectification is full-wave, so it is unlikely that both diodes have
failed, unless it's a tube rectifier, where the common cause for two diode
failures would be the heater, but we checked that all the heaters were glowing.
We can lose HT either because something in series has failed open circuit,
or because something has failed short circuit down to 0V. If an HT capacitor
had failed short circuit, it would have announced its failure with some noise
(explosion, fizzing, distorted sound plus hum from the loudspeakers). It is
far more likely that a series resistor or choke has failed.
Now that we know what we are looking for, we can switch off, unplug the amplifier
from the mains (leaving the plug in plain view), take the covers off and (carefully)
investigate. There could still be charged HT capacitors, so it's worth using
the DC voltage range of your DVM to check that they are discharged, but be
careful when probing inside even a notionally unpowered amplifier, more than
one piece of equipment has been destroyed by the slip of a probe. If capacitors
still retain charge, a 10 kOhm wirewound resistor is a handy way to discharge
them safely (see FIG. 3).
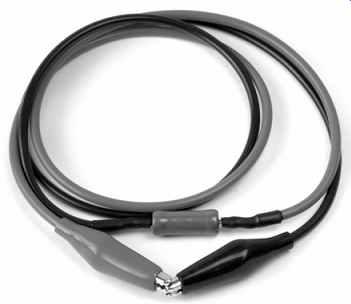
FIG. 3: A 10-kOhm 6W resistor with leads and insulated crocodile clips is
very handy for safely discharging capacitors
Quite apart from the fact that a capacitor's residual charge could give you
a nasty surprise, it would interfere with any attempt at resistance measurement
by your meter. Bear in mind that electrolytic capacitors suffer badly from
dielectric absorption, so leave your meter monitoring their voltage whilst
discharging.
You must pull the capacitor's voltage to well below 1V, and this can easily
take 20 seconds. Assuming that all the capacitors are discharged, we can use
the resistance range to check the HT choke and series HT resistors, and find
the problem quickly.
cont.>>
|